
You must make a design tradeoff between low switching losses (which require fast rise and fall times) and low EMI (which requires slow rise and fall times). To understand what is needed to drive the gate, you need to know how fast to switch the MOSFET. Similarly, when current is pulled out of the gate, that amount of current sets the MOSFET turn-off time. The amount of current provided to the gate determines how much time it takes to fully turn on the MOSFET. Even though the gate doesn’t conduct DC current, it does need current to charge and discharge the gate capacitance that turns the MOSFET on and off. Think of a power MOSFETs gate as a nonlinear capacitance between the gate and source terminals. It will switch faster, with a lower gate drive current, than one with a high Q G. A MOSFET with a lower Q G is easier to drive. The gate charge is a measure of how much charge you need to turn the MOSFET on and off. Once you find the necessary voltage rating and R DS(ON), be sure to consider the total gate charge (Q G ). This maximum allowable power dissipation drives the selection of the MOSFETs based on the R DS(ON) value. Thermal constraints, including the ambient temperature and any heatsinking available for the MOSFETs, set limits on how much power can be dissipated.

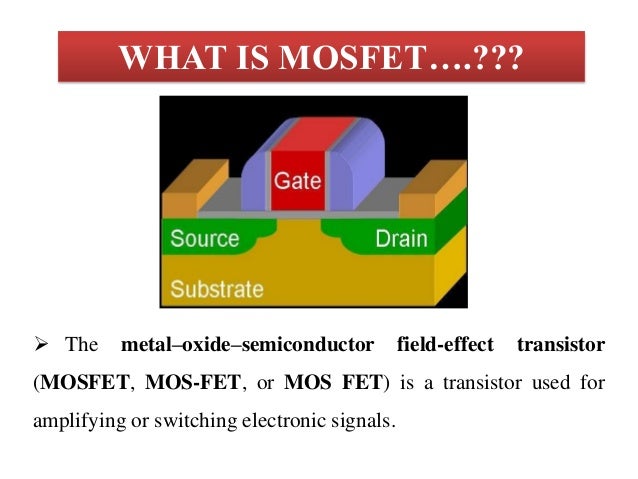
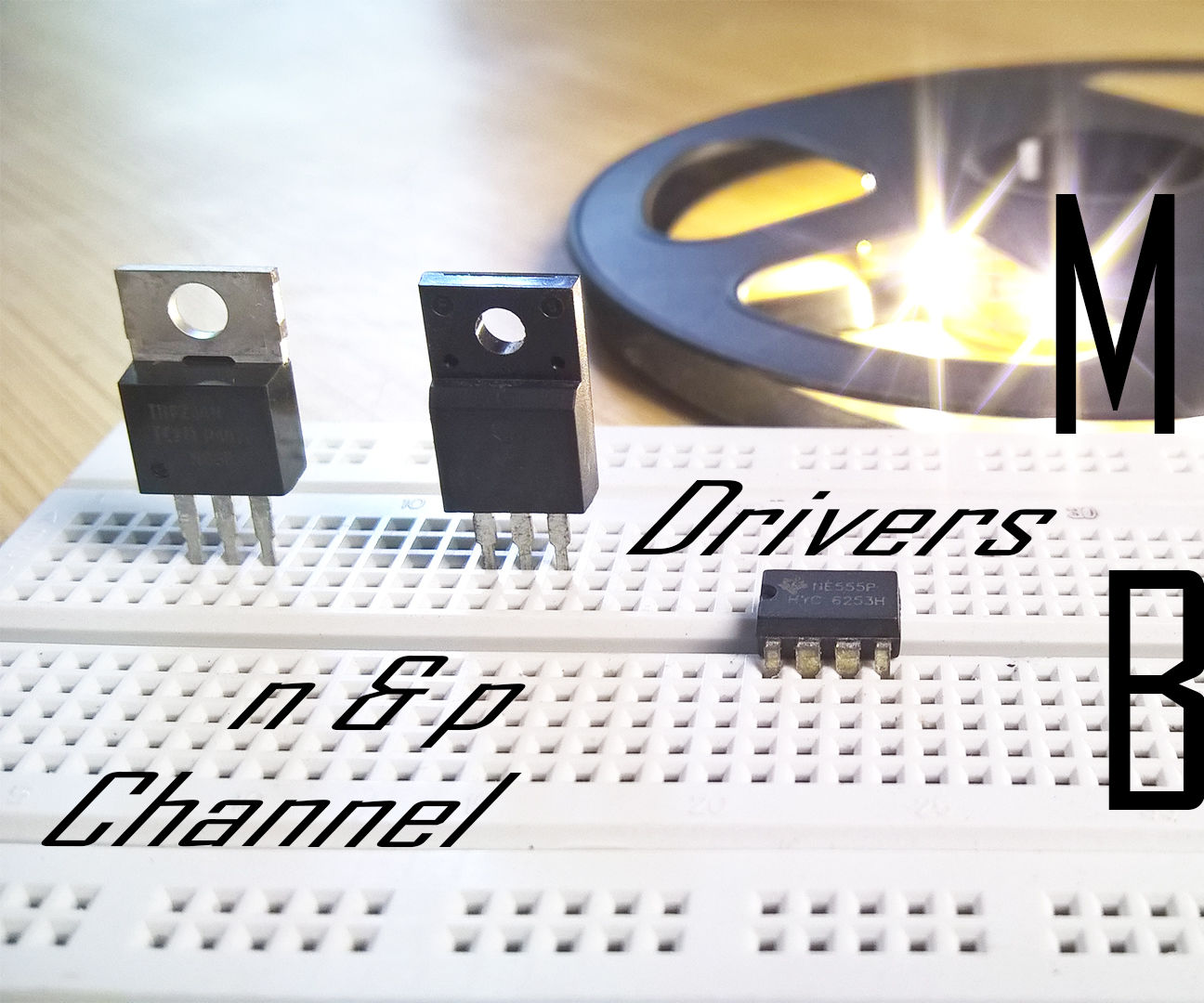
The MOSFETs dissipate power and generate heat in the drain-source resistance: R DS(ON). Of course, the MOSFET’s current rating must be high enough to provide the peak current that the motor needs, but usually thermal considerations dominate. In some cases-especially in systems with large currents, large torque steps, and poorly controlled power supplies-you may need a margin as much as twice the supply voltage. Remember that it is necessary to leave some margin.Ĭhoose a MOSFET whose drain-to-source voltage rating (V DS ) is at least 20% higher than the supply voltage. The maximum current requirement is usually set by the torque needed to start up the motor with a mechanical load.īe sure to choose power MOSFETs that are rated for at least the power supply voltage and the maximum current the motor requires. The drive must be powered from a voltage at least as high as that required to get the desired speed from the motor, but the supply voltage is often determined by the voltage available to the system. You can use the speed constant and torque constant-usually given in a motor’s datasheet-to estimate the voltage and current needed in a particular application.
